Precast hollow core slabs have revolutionized the construction industry, offering a fast, efficient, and cost-effective solution for creating floors and roofs in a wide range of buildings. This comprehensive guide will delve into the world of precast hollow core slabs, exploring their design principles, advantages, applications, manufacturing process, installation techniques, and considerations for architects and engineers.
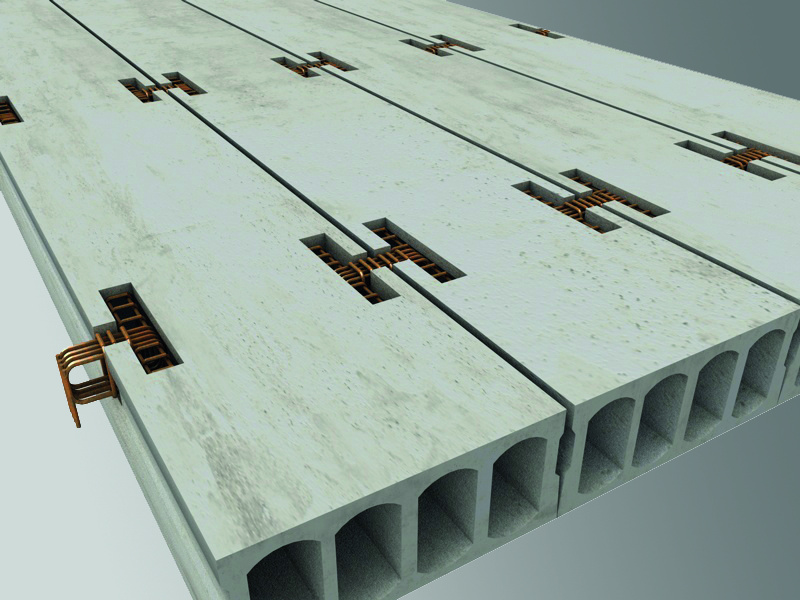
What are Precast Hollow Core Slabs?
Precast hollow core slabs are structural concrete elements manufactured off-site in a controlled factory environment. They are characterized by their longitudinal voids, or hollow cores, running throughout the length of the slab. These cores significantly reduce the weight of the slab without compromising its structural integrity, leading to numerous benefits in construction.
Key Features of Precast Hollow Core Slabs:
- Hollow Cores: The defining feature, these voids reduce the slab’s weight and allow for the passage of services like electrical wiring and plumbing.
- Pre-stressed Concrete: Typically, these slabs are pre-stressed, meaning high-strength steel tendons are tensioned before the concrete is poured. This imparts a compressive force into the concrete, increasing its load-bearing capacity and spanning capabilities.
- Variety of Sizes and Shapes: Hollow core slabs are available in a range of widths, depths, and lengths to suit various design requirements.
- Smooth Surface Finish: The factory-controlled production process ensures a consistent and smooth surface finish, reducing the need for extensive on-site finishing.
Why Choose Precast Hollow Core Slabs? Unveiling the Benefits
Precast hollow core slabs offer a multitude of advantages compared to traditional cast-in-place concrete and other flooring systems. Here’s a breakdown of the key benefits:
- Speed of Construction: This is perhaps the most significant advantage. Precast elements are manufactured concurrently with site preparation, allowing for rapid installation upon delivery. This drastically reduces construction timelines, leading to earlier project completion and cost savings.
- Reduced Labor Costs: The prefabrication process minimizes on-site labor requirements. With fewer workers needed for formwork, reinforcement, and pouring, labor costs are significantly reduced.
- Improved Quality Control: Factory production allows for strict quality control measures at every stage of the process. This ensures consistent dimensions, precise reinforcement placement, and optimal concrete curing, resulting in higher-quality and more durable slabs.
- Cost-Effectiveness: While the initial cost of precast slabs might seem higher than cast-in-place, the reduced construction time, lower labor costs, and minimized material wastage often result in overall cost savings. Furthermore, the long lifespan and low maintenance requirements of precast concrete contribute to long-term cost benefits.
- Reduced Formwork: Eliminating the need for extensive on-site formwork significantly reduces material costs and labor associated with its construction, dismantling, and cleaning.
- Increased Span Capabilities: The pre-stressed design of hollow core slabs allows for longer spans compared to traditional reinforced concrete slabs. This reduces the need for intermediate columns, creating more open and flexible interior spaces.
- Improved Sound Insulation: The hollow cores within the slabs can provide excellent sound insulation, reducing noise transmission between floors.
- Fire Resistance: Concrete is inherently fire-resistant, and precast hollow core slabs offer excellent fire protection, enhancing the safety of buildings.
- Reduced Environmental Impact: Precast construction minimizes on-site waste, reduces noise pollution, and can utilize recycled materials, contributing to a more sustainable construction process.
- Integration of Services: The hollow cores can be utilized to accommodate building services such as electrical wiring, plumbing, and HVAC ducts, simplifying installation and reducing the need for suspended ceilings.
- Design Flexibility: Precast hollow core slabs can be designed to accommodate various architectural features, including cantilevers, openings, and curved edges. This offers greater design flexibility compared to traditional concrete construction.
- Durability and Longevity: Precast concrete is highly durable and resistant to weathering, corrosion, and other environmental factors. This ensures a long service life and minimal maintenance requirements.
Applications of Precast Hollow Core Slabs: Where Can They Be Used?
The versatility of precast hollow core slabs makes them suitable for a wide range of applications, including:
- Residential Buildings: Apartments, condominiums, and single-family homes benefit from the speed of construction, sound insulation, and design flexibility offered by hollow core slabs.
- Commercial Buildings: Office buildings, retail spaces, and shopping centers utilize hollow core slabs for their large span capabilities, reduced column requirements, and rapid construction.
- Industrial Buildings: Warehouses, factories, and manufacturing plants benefit from the durability, fire resistance, and long span capabilities of hollow core slabs.
- Parking Structures: Hollow core slabs are commonly used in parking structures due to their durability, load-bearing capacity, and ease of installation.
- Schools and Universities: The sound insulation and fire resistance of hollow core slabs make them ideal for educational facilities.
- Hospitals and Healthcare Facilities: The clean and efficient construction process and the ability to integrate services make hollow core slabs suitable for healthcare environments.
- Bridges and Infrastructure: While less common than other precast elements, hollow core slabs can be adapted for certain bridge deck applications.
The Manufacturing Process: From Design to Delivery
Understanding the manufacturing process provides valuable insight into the quality and performance of precast hollow core slabs. Here’s a simplified overview:
- Design and Engineering: The process begins with detailed design and engineering calculations to determine the optimal slab dimensions, reinforcement requirements, and pre-stressing forces based on the specific project requirements.
- Mold Preparation: Reusable molds, typically made of steel, are meticulously prepared and cleaned. These molds define the shape and dimensions of the slab and the location of the hollow cores.
- Reinforcement Placement: High-strength steel tendons are placed within the mold according to the design specifications. These tendons are then tensioned using hydraulic jacks to impart the pre-stressing force. Additional reinforcement, such as steel mesh or rebar, may also be added for enhanced structural integrity.
- Concrete Pouring: High-quality concrete mix, specifically designed for precast applications, is carefully poured into the mold. Vibrators are used to consolidate the concrete and remove air pockets, ensuring a dense and uniform structure.
- Curing: The concrete is then cured in a controlled environment, typically using steam or hot water, to accelerate the hardening process and achieve the desired strength. Proper curing is critical for the durability and performance of the precast element.
- De-tensioning: Once the concrete has reached sufficient strength, the pre-stressing force in the tendons is gradually released, transferring the compressive force into the concrete slab.
- Demolding: The hardened slab is carefully removed from the mold.
- Finishing and Quality Control: The slab is inspected for any imperfections or defects. Minor repairs may be performed, and the surface finish may be refined. Rigorous quality control checks are conducted to ensure the slab meets all design specifications and industry standards.
- Storage and Transportation: The finished slabs are stored in a designated area until they are ready for transportation to the construction site. They are carefully loaded onto trucks and secured for safe delivery.
Installation Techniques: Ensuring a Smooth and Efficient Process
Proper installation is crucial for realizing the full benefits of precast hollow core slabs. Here’s a general overview of the installation process:
- Site Preparation: The supporting structure, such as walls or beams, must be properly prepared and leveled to ensure a stable base for the slabs.
- Lifting and Placement: Slabs are carefully lifted using cranes or other lifting equipment and positioned onto the supporting structure. The lifting points and procedures should be strictly followed to prevent damage to the slabs.
- Jointing and Grouting: The joints between the slabs are filled with a high-strength grout to create a continuous and monolithic floor or roof structure. The grouting process should be carefully controlled to ensure proper filling and consolidation of the grout.
- Connection Details: Connections between the slabs and the supporting structure are typically achieved using steel connectors, such as dowels or shear keys, which are embedded in the concrete and anchored to the supporting structure. The connection details should be carefully designed to ensure adequate load transfer and structural integrity.
- Post-Tensioning (Optional): In some cases, post-tensioning may be applied to the slabs after they have been installed to further enhance their load-bearing capacity and reduce deflections.
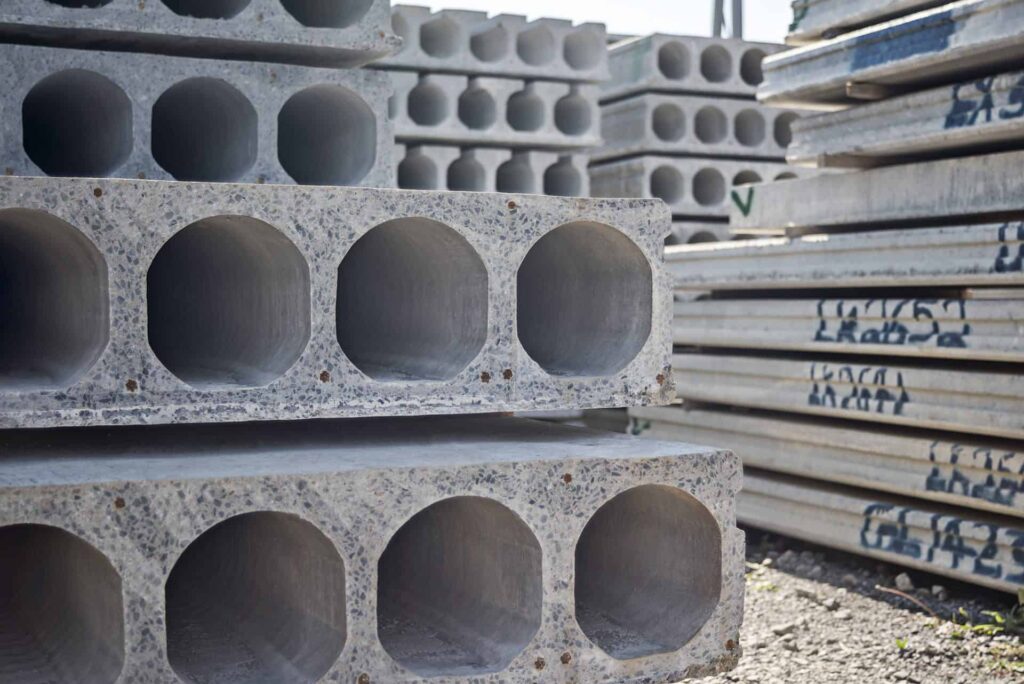
Design Considerations for Architects and Engineers: A Comprehensive Guide
Designing with precast hollow core slabs requires a thorough understanding of their structural behavior, load-carrying capacity, and connection details. Here are some key design considerations for architects and engineers:
- Span and Load Requirements: The slab’s span and load-carrying capacity must be carefully calculated based on the intended use of the building and the applicable building codes. Factors such as live load, dead load, and impact load should be considered.
- Deflection Limits: Deflection limits should be established to ensure that the floor or roof structure remains aesthetically pleasing and does not interfere with the functionality of the building. Deflection calculations should consider both short-term and long-term effects.
- Shear Capacity: The shear capacity of the slab must be adequate to resist shear forces induced by applied loads. Shear reinforcement may be required in certain areas of the slab, particularly near supports.
- Connection Details: The design of the connections between the slabs and the supporting structure is critical for ensuring adequate load transfer and structural integrity. The connection details should be carefully designed to resist shear forces, bending moments, and tensile forces.
- Fire Resistance: The fire resistance of the slab should be determined based on the applicable building codes. The concrete cover over the reinforcement and the type of concrete used can significantly affect the fire resistance of the slab.
- Acoustic Performance: The acoustic performance of the slab should be considered, particularly in residential and commercial buildings. The hollow cores within the slab can provide excellent sound insulation, but additional measures may be required to meet specific acoustic requirements.
- Service Integration: The hollow cores can be utilized to accommodate building services such as electrical wiring, plumbing, and HVAC ducts. The design should consider the size and location of these services to ensure that they can be easily installed and maintained.
- Camber and Tolerances: Precast hollow core slabs are typically manufactured with a slight upward curvature, known as camber, to compensate for deflections under load. The design should consider the camber of the slabs and the allowable tolerances for dimensions and alignment.
- Construction Tolerances: Account for construction tolerances in the design and installation process. These tolerances can affect the overall dimensions and alignment of the structure. Proper planning and coordination are essential to minimize the impact of construction tolerances.
- Transportation and Handling: The design should consider the transportation and handling requirements of the slabs. The lifting points and procedures should be clearly specified to prevent damage during transportation and installation.
- Code Compliance: Ensure that the design complies with all applicable building codes and standards. Local regulations may vary, so it is important to consult with local authorities and obtain the necessary permits.
Hollow Core Slabs vs. Other Flooring Systems: A Comparative Analysis
To fully appreciate the benefits of precast hollow core slabs, it’s helpful to compare them to other common flooring systems:
- Cast-in-Place Concrete: While cast-in-place concrete offers design flexibility, it requires extensive formwork, is more labor-intensive, and takes longer to cure. Precast hollow core slabs offer faster construction and improved quality control.
- Steel Decking: Steel decking is lightweight and relatively quick to install, but it often requires additional fireproofing and sound insulation. Hollow core slabs provide inherent fire resistance and sound insulation properties.
- Timber Flooring: Timber flooring is aesthetically pleasing but may require more maintenance and is susceptible to fire and moisture damage. Hollow core slabs are durable, fire-resistant, and require minimal maintenance.
Conclusion: Embracing the Future of Construction with Precast Hollow Core Slabs
Precast hollow core slabs offer a compelling solution for modern construction, providing a balance of speed, efficiency, cost-effectiveness, and design flexibility. By understanding the design principles, manufacturing process, and installation techniques, architects and engineers can leverage the benefits of this innovative technology to create high-quality, sustainable, and long-lasting buildings. As the construction industry continues to evolve, precast hollow core slabs are poised to play an increasingly important role in shaping the built environment. Embracing this technology can lead to significant improvements in project delivery, cost savings, and overall building performance.
Call to Action:
- Contact a Precast Manufacturer: Reach out to a reputable precast concrete manufacturer to discuss your specific project requirements and obtain a customized solution.
- Consult with a Structural Engineer: Engage a structural engineer experienced in precast concrete design to ensure the structural integrity and safety of your building.
- Explore Case Studies: Review case studies of successful projects that have utilized precast hollow core slabs to gain inspiration and insights.
By taking these steps, you can unlock the full potential of precast hollow core slabs and create buildings that are both aesthetically pleasing and structurally sound.