Precast concrete panels are concrete elements that are manufactured off-site in a controlled factory environment and then transported to the construction site for installation. This method offers numerous advantages in terms of speed, quality control, and design flexibility, making them a popular choice for various building applications.
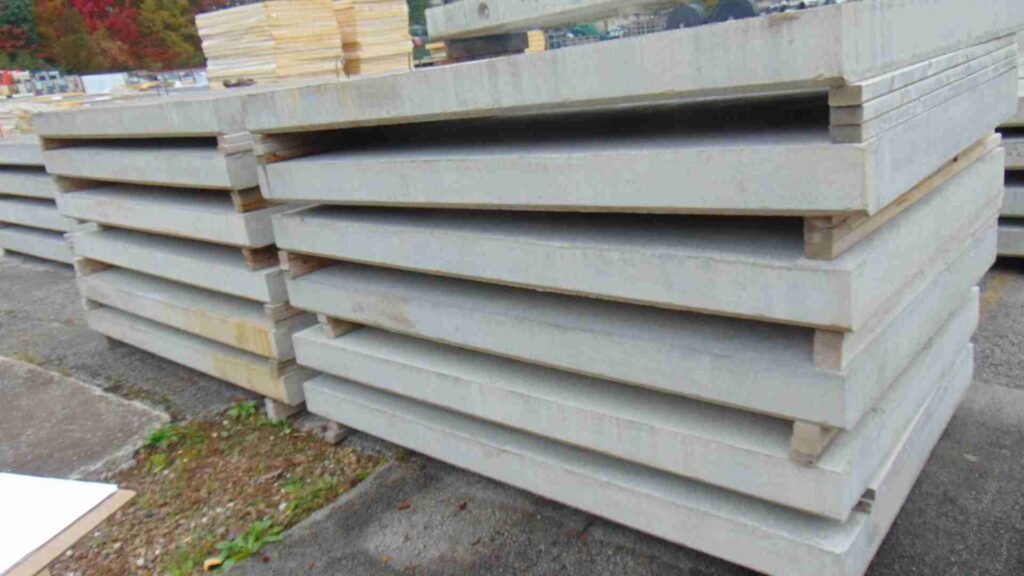
Detailed Description:
- Manufacturing Process:
- Formwork Preparation: Molds, or forms, are prepared to the exact dimensions and shapes of the desired panels. These forms can be made of steel, wood, or fiberglass.
- Reinforcement Placement: Steel reinforcing bars (rebar), wire mesh, or other reinforcement materials are placed within the forms to provide tensile strength and improve the panel’s structural integrity.
- Embeds and Inserts: Any necessary embeds, such as lifting anchors, connection plates, or openings for windows and doors, are placed within the forms before concrete placement.
- Concrete Placement: Concrete is poured into the forms and consolidated using vibration to eliminate air pockets and ensure proper compaction.
- Curing: The concrete is cured in a controlled environment, typically with temperature and humidity control, to achieve optimal strength and durability.
- Form Removal: Once the concrete has reached sufficient strength, the forms are removed.
- Finishing: The panels are inspected, and any necessary finishing operations, such as grinding, polishing, sandblasting, or coating, are performed to achieve the desired aesthetic appearance.
- Types of Precast Panels:
- Solid Panels: Simple, solid concrete panels used for walls, floors, and roofs.
- Sandwich Panels: Consist of two layers of concrete with an insulating core in between (e.g., expanded polystyrene (EPS) or mineral wool). Provide excellent thermal performance.
- Ribbed Panels: Have ribs or fins on one side to increase their strength-to-weight ratio.
- Hollow-Core Panels: Contain longitudinal voids or cores to reduce weight and provide space for utilities.
- Architectural Panels: Designed with specific aesthetic features, such as exposed aggregate, textured surfaces, or intricate patterns.
- Thin Brick Faced Panels: Precast concrete panels with thin brick cast into the face to replicate the look of traditional brickwork.
- Stone Faced Panels: Simlar to thin brick, but using natural stone or manufactured stone veneer.
- Functions of Precast Panels:
- Cladding/Façade: Providing an exterior skin for buildings, offering weather protection and architectural aesthetics.
- Load-Bearing Walls: Supporting vertical loads from the roof and upper floors.
- Shear Walls: Resisting lateral loads from wind or earthquakes.
- Floor Slabs: Forming the horizontal surfaces of floors and roofs.
- Bridge Decks: Providing the driving surface for bridges.
- Retaining Walls: Holding back soil or other materials at different elevations.
- Sound Barriers: Reducing noise pollution along highways and railways.
Advantages of Precast Concrete Panels:
- Faster Construction: Manufacturing panels off-site significantly reduces on-site construction time.
- Improved Quality Control: The controlled factory environment allows for consistent and high-quality production.
- Design Flexibility: Precast concrete can be molded into virtually any shape and size, allowing for a wide range of architectural designs.
- Durability: Concrete is a durable material that can withstand harsh weather conditions and resist deterioration over time.
- Fire Resistance: Concrete is naturally fire-resistant, providing excellent protection against fire damage.
- Sound Insulation: Precast panels provide good sound insulation, reducing noise transmission between spaces.
- Energy Efficiency: Sandwich panels with insulation can significantly improve a building’s energy performance.
- Reduced On-Site Labor: The amount of on-site labor required is reduced, lowering construction costs.
- Less Material Waste: Precast production minimizes material waste compared to traditional cast-in-place construction.
- Aesthetic Versatility: A wide range of finishes and textures can be applied to precast panels to create visually appealing facades.
- All-Weather Construction: Manufacturing in a controlled environment allows for year-round production, regardless of weather conditions.
- Long Spans: Precast panels, especially prestressed panels, can achieve long spans with minimal intermediate supports.
Disadvantages of Precast Concrete Panels:
- High Initial Cost: The initial cost of precast panels can be higher than that of some other materials.
- Transportation Costs: Transportation costs can be significant, especially for large or heavy panels.
- Crane Access: Requires crane access for lifting and installing the panels.
- Connection Details: Connection details must be carefully designed to ensure structural integrity and prevent water leakage.
- Joint Visibility: Joints between panels can be visible, which may be undesirable for some architectural designs.
- Limited On-Site Modifications: Making modifications to precast panels on-site can be difficult and expensive.
- Requires Careful Planning: The entire process requires very careful planning and coordination as changes are difficult after panels are cast.
Key Considerations for Using Precast Panels:
- Early Collaboration: Architects, engineers, and precast manufacturers should collaborate early in the design process.
- Accurate Dimensions: Accurate dimensions are crucial for proper fit and alignment of the panels.
- Connection Details: Connection details should be carefully designed and reviewed by a structural engineer.
- Transportation Planning: Plan the transportation of the panels to the site well in advance.
- Installation Sequencing: Develop a detailed installation sequence to ensure efficient and safe erection.
- Quality Control: Implement a rigorous quality control program throughout the manufacturing and installation process.
- Joint Sealing: Properly seal joints between panels to prevent water leakage.
Applications of Precast Panels:
- High-Rise Buildings: Cladding for high-rise buildings, providing a durable and aesthetically pleasing exterior.
- Office Buildings: Exterior walls for office buildings.
- Commercial Buildings: Walls, floors, and roofs for retail stores, shopping malls, and warehouses.
- Industrial Buildings: Walls and roofs for factories and manufacturing plants.
- Apartment Buildings: Walls and floors for apartment buildings and condominiums.
- Parking Garages: Walls and floors for parking structures.
- Bridges: Bridge decks and parapets.
- Retaining Walls: Walls for holding back soil or other materials.
- Sound Barriers: Barriers for reducing noise pollution along highways and railways.
Trends and Innovations:
- Ultra-High-Performance Concrete (UHPC): Using UHPC to create thinner, lighter, and stronger panels.
- 3D Printing of Molds: Using 3D printing to create complex and custom mold shapes.
- Self-Cleaning Concrete: Applying self-cleaning coatings to precast panels to reduce maintenance.
- Smart Panels: Embedding sensors into precast panels to monitor structural health and performance.
- Sustainable Precast: Using recycled aggregates and supplementary cementitious materials to reduce the environmental impact of precast production.
- BIM Integration: Integrating precast design and manufacturing with Building Information Modeling (BIM) for improved coordination and accuracy.
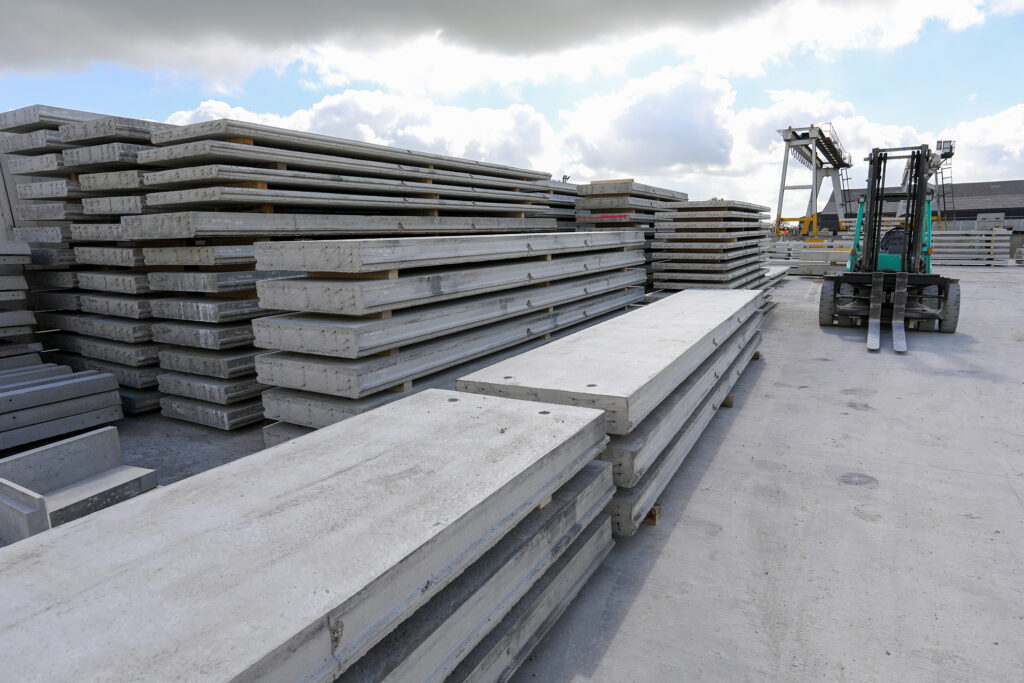
In conclusion, precast concrete panels are a versatile and efficient building material that offers numerous advantages for a wide range of applications. With careful planning, design, and execution, precast panels can provide a cost-effective, durable, and aesthetically pleasing solution for your next construction project. Consider consulting with a qualified structural engineer and experienced precast manufacturer to ensure the success of your project.