Precast concrete beams and columns are structural elements manufactured off-site in a controlled factory environment and then transported to the construction site for assembly. This method offers significant advantages in terms of speed, quality control, and design flexibility, making them a popular choice for a wide range of building applications.
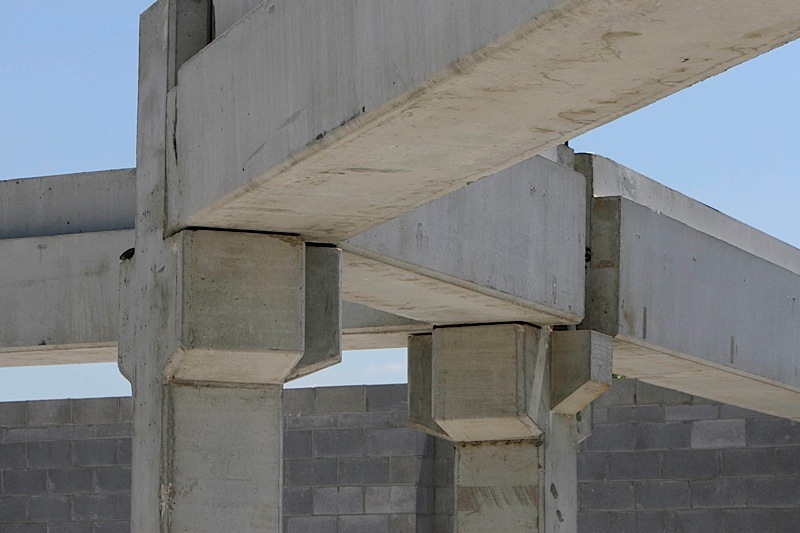
Detailed Description:
- Manufacturing Process:
- Formwork Preparation: Molds, or forms, are precisely prepared to the specific dimensions and shapes of the desired beams and columns. These forms are typically made of steel for durability and precision.
- Reinforcement Placement: Steel reinforcing bars (rebar) are carefully placed within the forms according to the structural engineer’s design. The rebar provides tensile strength and shear resistance to the concrete elements. For prestressed elements, high-strength steel strands or tendons are also positioned within the forms and tensioned.
- Embeds and Inserts: Any necessary embeds, such as connection plates, lifting anchors, or other hardware, are strategically placed within the forms before the concrete is poured. These embeds facilitate connections to other structural elements.
- Concrete Placement: High-quality concrete is poured into the forms and consolidated using vibration to eliminate air pockets and ensure proper compaction around the reinforcement.
- Curing: The concrete is cured in a controlled environment to achieve optimal strength and durability. Temperature and humidity are carefully monitored to promote proper hydration of the cement. For prestressed elements, the tension in the steel strands is released after the concrete has reached sufficient strength, transferring the compressive force to the concrete.
- Form Removal: Once the concrete has reached the required strength, the forms are carefully removed.
- Finishing and Inspection: The precast elements are thoroughly inspected for any defects. Minor imperfections may be repaired, and any necessary finishing operations, such as surface smoothing or application of protective coatings, are performed.
- Types of Precast Beams:
- Rectangular Beams: Simple, rectangular-shaped beams commonly used for shorter spans.
- T-Beams: Beams with a T-shaped cross-section, providing increased strength and stiffness.
- Inverted T-Beams: T-beams with the flange on the bottom, often used for edge beams or spandrel beams.
- L-Beams: Beams with an L-shaped cross-section, used as edge beams or to support cantilevered slabs.
- I-Beams: Beams with an I-shaped cross-section, offering a high strength-to-weight ratio and suitable for longer spans.
- Prestressed Beams: Beams that are prestressed before being subjected to service loads, increasing their load-carrying capacity and reducing deflections.
- Types of Precast Columns:
- Rectangular Columns: Simple, rectangular-shaped columns commonly used for low-rise buildings.
- Square Columns: Square-shaped columns offering equal strength in both directions.
- Circular Columns: Circular-shaped columns providing aesthetic appeal and uniform strength.
- Prestressed Columns: Columns that are prestressed to increase their load-carrying capacity and prevent cracking.
- Advantages of Precast Beams and Columns:
- Faster Construction: Manufacturing off-site significantly reduces on-site construction time.
- Improved Quality Control: The controlled factory environment allows for consistent and high-quality production, ensuring uniform dimensions and material properties.
- High Strength and Durability: Precast elements are made with high-quality concrete and reinforcement, resulting in strong and durable structural members.
- Long Spans: Prestressed beams can achieve long spans with minimal intermediate supports, allowing for greater design flexibility.
- Reduced Formwork Costs: The use of reusable steel forms reduces the need for on-site formwork, saving time and money.
- Reduced On-Site Labor: The amount of on-site labor required for beam and column construction is reduced, lowering labor costs.
- All-Weather Construction: Manufacturing in a controlled environment allows for year-round production, regardless of weather conditions.
- Design Flexibility: Precast elements can be designed with a variety of shapes, sizes, and finishes to meet specific architectural requirements.
- Fire Resistance: Concrete is naturally fire-resistant, providing excellent protection against fire damage.
- Seismic Resistance: Precast beams and columns can be designed to resist seismic forces, providing enhanced safety in earthquake-prone areas.
- Sustainability: The use of recycled aggregates and supplementary cementitious materials can reduce the environmental impact of precast production.
- Disadvantages of Precast Beams and Columns:
- High Initial Cost: The initial cost of precast elements can be higher than that of some other materials.
- Transportation Costs: Transportation costs can be significant, especially for large or heavy beams and columns.
- Crane Access: Requires crane access for lifting and installing the beams and columns.
- Connection Details: Connection details must be carefully designed to ensure structural integrity and prevent water leakage.
- Limited On-Site Modifications: Making modifications to precast elements on-site can be difficult and expensive.
- Requires Careful Planning: The entire process requires very careful planning and coordination, as changes are difficult after the beams and columns are cast.
- Connection Types:
- Bolted Connections: Steel plates are cast into the ends of the beams and columns, and the elements are connected using bolts.
- Welded Connections: Steel plates are cast into the ends of the beams and columns, and the elements are connected by welding the plates together.
- Grouted Connections: Grout is used to fill the space between the ends of the beams and columns, creating a strong and durable connection.
- Dowel Connections: Steel dowels are inserted into holes in the ends of the beams and columns, and the space is filled with grout.
- Applications of Precast Beams and Columns:
- Bridges: Supporting bridge decks and approaches.
- Parking Garages: Providing structural support for parking structures.
- Office Buildings: Framing for office buildings, allowing for open floor plans.
- Industrial Buildings: Supporting roofs and floors in factories and warehouses.
- Schools: Constructing school buildings quickly and efficiently.
- Hospitals: Creating durable and fire-resistant hospital structures.
- Apartment Buildings: Framing for multi-story apartment buildings.
- Warehouses: Creating open spaces and high ceilings in warehouses.
- Design Considerations:
- Load Analysis: Determining the dead loads, live loads, wind loads, and seismic loads that the beams and columns will be subjected to.
- Structural Analysis: Analyzing the beams and columns to determine the bending moments, shear forces, and axial forces.
- Reinforcement Design: Selecting the appropriate size, spacing, and placement of steel reinforcement to resist the internal forces.
- Connection Design: Designing the connections between beams and columns to ensure adequate strength and stability.
- Deflection Control: Ensuring that the beams and columns do not deflect excessively under load.
- Fire Resistance: Designing the beams and columns to meet the required fire resistance ratings.
- Code Compliance: Ensuring that the design complies with all applicable building codes and standards.
- Trends and Innovations:
- Ultra-High-Performance Concrete (UHPC): Using UHPC to create lighter, stronger, and more durable beams and columns.
- Self-Consolidating Concrete (SCC): Simplifies concrete placement and improves the quality of the finished product.
- Carbon Fiber Reinforcement: Replacing steel rebar with carbon fiber reinforcement to reduce weight and improve corrosion resistance.
- Building Information Modeling (BIM): Facilitates collaboration and improves design accuracy.
- Automated Manufacturing: Using automated manufacturing processes to increase efficiency and reduce costs.
- Modular Construction: Combining precast beams and columns with other precast elements to create modular building systems.
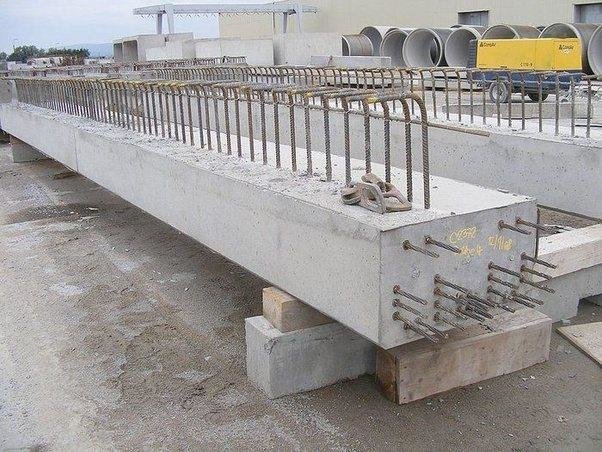
In conclusion, precast concrete beams and columns are a versatile and efficient building material that offers numerous advantages for a wide range of applications. With careful planning, design, and execution, precast construction can provide a cost-effective, durable, and aesthetically pleasing solution for your next project. Consult with qualified structural engineers and experienced precast manufacturers to ensure a successful project.