Concrete Masonry Units (CMUs), commonly known as concrete blocks, are a ubiquitous building material renowned for their versatility, durability, and affordability. CMU structures have formed the backbone of countless buildings, from humble homes to towering skyscrapers. This comprehensive guide will delve deep into the world of CMU structures, exploring their design principles, construction methods, advantages, applications, and crucial considerations for architects, engineers, and builders looking to leverage their full potential.
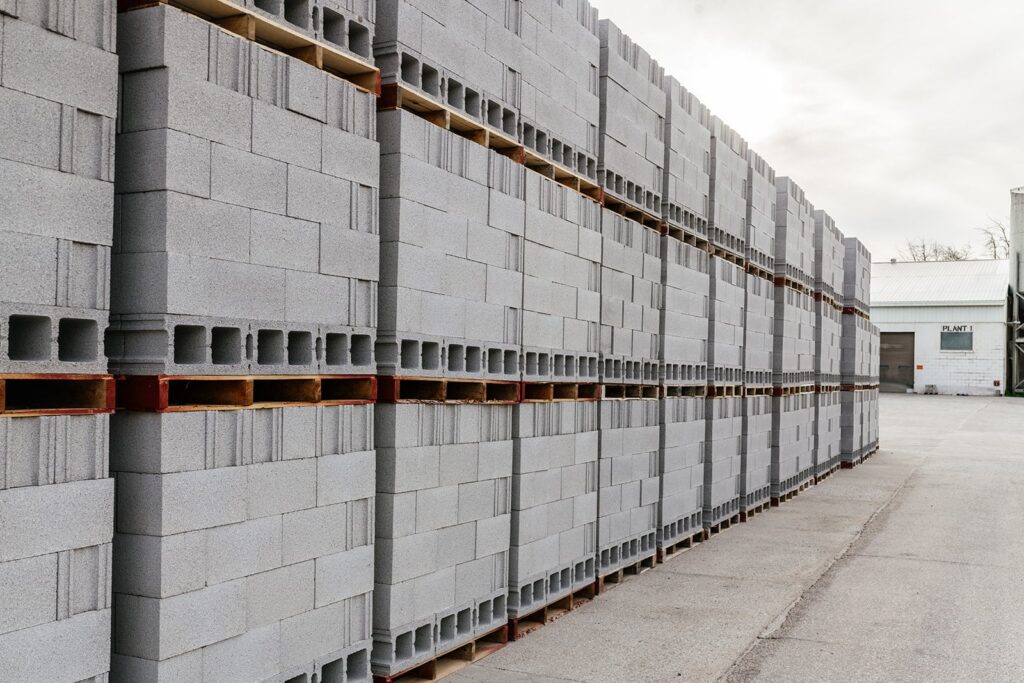
What are Concrete Masonry Units (CMUs)? A Fundamental Overview
Concrete Masonry Units (CMUs) are precast concrete blocks manufactured to precise dimensions and standardized shapes. They are primarily composed of Portland cement, aggregates (typically sand and gravel or crushed stone), and water. Sometimes, admixtures are added to enhance specific properties, such as workability, durability, or color. The mix is molded into the desired shape and cured to achieve its final strength.
Key Characteristics of CMUs:
- Standard Sizes: CMUs are typically manufactured in nominal sizes, with the most common being 8 x 8 x 16 inches (actual dimensions are slightly smaller to account for mortar joints). Other sizes are available to suit specific design needs.
- Variety of Shapes: Besides the standard rectangular block, CMUs come in a variety of shapes, including bond beam blocks, lintel blocks, corner blocks, and jamb blocks, designed for specific applications within a wall system.
- Different Weights: CMUs are available in different weights, including lightweight, medium-weight, and normal-weight options. Lightweight blocks offer advantages in terms of handling and transportation, while heavier blocks provide greater structural capacity and sound insulation.
- Textural Finishes: CMUs can be manufactured with various surface textures, ranging from smooth to split-face, ribbed, or scored, providing architectural flexibility and aesthetic appeal.
- Color Options: While the standard color is gray, CMUs can be integrally colored during the manufacturing process or painted or stained after installation to achieve a desired aesthetic.
Advantages of Building with CMUs: A Compelling Case
CMU construction offers a compelling combination of advantages that make it a popular choice for a wide range of building projects. Here’s a detailed look at the benefits:
- CMUs are incredibly durable and resistant to weathering, fire, insects, and decay. CMU structures can withstand harsh environmental conditions and provide a long service life, making them a cost-effective investment in the long run.
- CMUs possess high compressive strength, making them suitable for load-bearing walls and structural applications. CMU walls provide excellent lateral stability, resisting wind and seismic forces.
- Concrete is inherently fire-resistant, and CMU walls offer excellent fire protection, providing valuable time for occupants to escape in the event of a fire. Fire-resistance ratings can be achieved by specifying the appropriate CMU thickness and mortar type.
- The mass and density of CMUs provide excellent sound insulation, reducing noise transmission between spaces. CMU walls can effectively dampen sound from both exterior and interior sources, creating a quieter and more comfortable environment.
- CMUs are a relatively inexpensive building material compared to other options like brick, stone, or cast-in-place concrete. Their standardized sizes and ease of installation contribute to lower labor costs and overall project savings.
- CMUs offer considerable design flexibility. They can be used to create a variety of wall patterns, textures, and colors. Their modular nature allows for easy integration with other building systems and components.
- CMU construction is relatively straightforward, requiring basic masonry skills. CMUs are easy to handle and install, and the mortar joints provide flexibility in accommodating minor variations in dimensions.
- CMUs are readily available in most regions, ensuring a reliable supply and minimizing delays. A network of CMU manufacturers and suppliers provides access to a wide range of products and technical support.
- CMUs can contribute to sustainable building practices. They can be manufactured using recycled materials, and their durability reduces the need for frequent replacement. CMU walls can also provide thermal mass, reducing heating and cooling loads.
- CMUs are incredibly versatile and can be used for a wide range of applications, from load-bearing walls and partitions to foundation walls and retaining walls. They can be used in both residential and commercial construction.
Applications of CMU Structures: Where Can You Use Them?
The versatility of CMUs makes them suitable for a wide range of applications across various building types:
- CMUs are commonly used for load-bearing walls in residential, commercial, and industrial buildings. They provide the structural support needed to carry roof and floor loads.
- CMUs are an excellent choice for foundation walls due to their durability and resistance to moisture penetration. They provide a stable and long-lasting foundation for buildings.
- CMUs are used for partition walls in both residential and commercial buildings to create separate spaces and provide sound insulation.
- CMUs can be used to construct retaining walls to support soil and prevent erosion. They provide a stable and durable solution for managing grade changes.
- CMU walls are frequently used as fire walls to separate buildings or areas within a building to prevent the spread of fire.
- CMU walls are often used to construct elevator and stair shafts due to their fire resistance and structural stability.
- CMUs are a popular choice for schools and gymnasiums due to their durability, sound insulation, and fire resistance.
- CMUs are well-suited for warehouses and industrial buildings due to their strength, durability, and affordability.
- CMUs are frequently used in multi-family housing projects due to their sound insulation and fire resistance, creating a comfortable and safe living environment.
- CMUs are often used as infill walls within steel or concrete frame structures, providing a durable and cost-effective enclosure.
Designing with CMUs: Key Considerations for Architects and Engineers
Designing with CMUs requires a thorough understanding of their structural properties, detailing requirements, and the applicable building codes. Here are some key design considerations:
- CMU walls must be designed to resist all applied loads, including gravity loads, wind loads, seismic loads, and lateral soil pressure. Structural calculations should be performed to determine the required CMU thickness, reinforcement, and mortar type.
- The type of mortar used to join CMUs significantly affects the wall’s strength, durability, and water resistance. The appropriate mortar type should be selected based on the design requirements and the exposure conditions.
- Reinforcement is typically required in CMU walls to increase their strength and resistance to cracking. Vertical and horizontal reinforcement should be placed in accordance with the design specifications.
- Grouting the cores of CMU walls can significantly increase their strength and stability. Grouting is typically required in load-bearing walls and walls subjected to high lateral loads.
- The bond pattern used to lay CMUs affects the appearance and structural performance of the wall. Common bond patterns include running bond, stack bond, and English bond.
- Control joints are intentionally weakened planes in CMU walls that allow for movement due to thermal expansion and contraction, preventing cracking. Control joints should be properly located and detailed to ensure their effectiveness.
- Expansion joints are wider gaps in CMU walls that allow for larger movements due to thermal expansion and contraction. Expansion joints are typically required in long walls or walls subjected to significant temperature variations.
- Lintels and beams are used to span openings in CMU walls, such as doors and windows. They must be designed to carry the loads above the opening and transfer them to the adjacent CMU walls.
- CMU walls are porous and can absorb water. Proper detailing and water-resistant coatings are essential to prevent moisture penetration and damage.
- The thermal performance of CMU walls can be improved by adding insulation. Insulation can be placed within the cores of the CMUs, on the exterior surface of the wall, or within a cavity wall system.
- The acoustic performance of CMU walls can be enhanced by using sound-absorbing materials or by increasing the wall thickness.
- All CMU structures must comply with applicable building codes and standards. It is important to consult with local authorities and obtain the necessary permits before starting construction.
Construction Methods for CMU Structures: A Step-by-Step Guide
Constructing CMU structures requires careful planning, skilled labor, and adherence to proper construction techniques. Here’s a general overview of the construction process:
- Foundation Preparation: The foundation must be properly prepared and leveled to provide a stable base for the CMU walls.
- Mortar Mixing: The mortar should be mixed according to the manufacturer’s instructions. The consistency of the mortar is crucial for achieving proper bond and water resistance.
- Laying the First Course: The first course of CMUs should be carefully laid on a bed of mortar, ensuring that the blocks are level and aligned.
- Building the Wall: Subsequent courses of CMUs are laid on top of the first course, using a running bond pattern or other approved bond pattern. Mortar is applied to the head and bed joints, and the blocks are carefully aligned.
- Reinforcement Placement: Vertical and horizontal reinforcement is placed in accordance with the design specifications.
- Grouting (If Required): If grouting is required, the cores of the CMUs are filled with grout after the mortar has set.
- Lintel and Beam Installation: Lintels and beams are installed over openings in the CMU walls.
- Control Joint and Expansion Joint Installation: Control joints and expansion joints are installed at the locations specified in the design drawings.
- Wall Finishing: The CMU walls can be finished with paint, stucco, or other coatings to protect them from the elements and enhance their appearance.
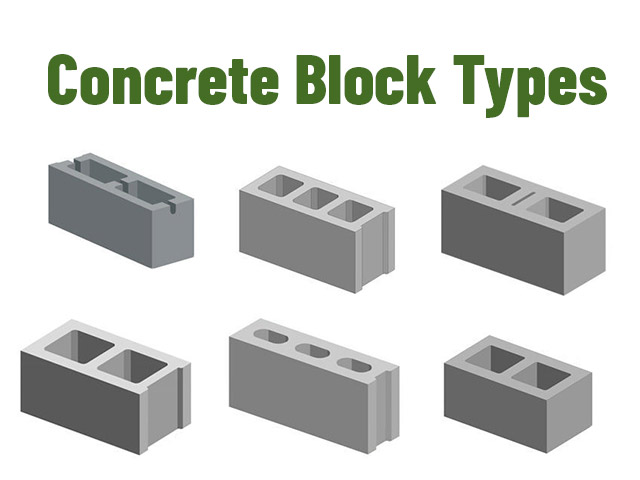
Common Problems and Solutions in CMU Construction:
- Cracking: Cracking is a common problem in CMU walls, often caused by thermal movement, settlement, or inadequate reinforcement. Solutions include proper control joint placement, adequate reinforcement, and proper foundation design.
- Moisture Penetration: Moisture penetration can lead to efflorescence, staining, and deterioration of CMU walls. Solutions include proper flashing, water-resistant coatings, and adequate drainage.
- Efflorescence: Efflorescence is a white, powdery deposit that can appear on CMU walls, caused by the migration of salts to the surface. Solutions include using low-alkali cement, preventing moisture penetration, and applying a cleaner to remove the efflorescence.
- Inadequate Bond: Inadequate bond between CMUs and mortar can lead to reduced strength and water resistance. Solutions include using the correct mortar type, properly mixing the mortar, and ensuring that the CMUs are clean and dry before laying.
CMU vs. Other Wall Systems: A Comparative Analysis
To fully appreciate the benefits of CMU construction, it’s helpful to compare it to other common wall systems:
Feature | CMU Walls | Wood Frame Walls | Steel Frame Walls | Cast-in-Place Concrete Walls |
Durability | High | Moderate (susceptible to rot and insects) | Moderate (susceptible to corrosion) | High |
Fire Resistance | Excellent | Low | Moderate (requires fireproofing) | Excellent |
Sound Insulation | Excellent | Moderate (requires additional insulation) | Moderate (requires additional insulation) | Good |
Cost | Moderate | Low | Moderate | High |
Construction Time | Moderate | Fast | Moderate | Slow |
Design Flexibility | Good | Good | Good | Moderate |
Sustainability | Good (can use recycled materials) | Moderate (renewable resource, but can contribute to deforestation) | Moderate (recyclable, but energy-intensive to produce) | High (durable, but energy-intensive to produce) |
Conclusion: CMU Structures – A Timeless and Reliable Building Solution
Concrete Masonry Unit (CMU) structures offer a compelling combination of durability, strength, affordability, and design flexibility, making them a timeless and reliable building solution for a wide range of applications. By understanding the design principles, construction methods, and key considerations outlined in this guide, architects, engineers, and builders can leverage the full potential of CMUs to create high-quality, sustainable, and long-lasting buildings. As the construction industry continues to evolve, CMU structures will undoubtedly remain a cornerstone of the built environment.
Call to Action:
- Consult with a Masonry Expert: Consult with a qualified masonry contractor or engineer to discuss your specific project requirements and ensure proper design and construction.
- Visit a CMU Manufacturing Facility: Visit a local CMU manufacturing facility to learn more about the manufacturing process and available product options.
- Review CMU Project Case Studies: Review case studies of successful CMU projects to gain inspiration and insights.
By taking these steps, you can make informed decisions about using CMU structures in your next building project and create durable, aesthetically pleasing, and cost-effective buildings that stand the test of time.